Foratura rapida e precisa con rilevamento affidabile dello sfondamento della parete. Rilevamento accurato senza interferenze
Rilevamento efficace dello sfondamento della parete
senza impingement della parete posteriore
I fori nelle pale della turbina o nelle palette restano fondamentali per evitare il surriscaldamento durante l’uso del motore. Uno dei processi più importanti è la produzione dei fori di raffreddamento critici di questi componenti di turbine e motori a reazione. Per quanto riguarda le tecnologie di produzione di queste parti strategiche come la struttura cava risultante dalla fusione, la foratura per elettroerosione di questi fori è sempre stata un passo importante con la considerazione della lavorazione a impatto senza parete posteriore o, più in generale, del risultato della sovraforatura. Oggi il processo di fusione migliorato può fornire cavità interne complesse con profili stretti di circa 0,5 mm di larghezza. Le variazioni di fusione all’interno della struttura cava sono sempre possibili e aumentano le difficoltà del processo di perforazione, per mantenere l’elettrodo dalla breve cavità di ingresso ed evitare di toccare la parete posteriore.
Sulla base di una lunga esperienza e di un know-how tecnologico sul perfetto controllo della lavorazione dei fori, noi di SARIX abbiamo introdotto, fin dalla nostra fondazione, il generatore SX-MPS con un software di controllo per il rilevamento dell’elettrodo di rottura efficace e preciso. Il controllore di foratura Micro EDM avanzato consente un servosensibile fine per rilevare qualsiasi variazione dei parametri durante la foratura della cavità della parete.
Rilevamento efficace dello sfondamento senza contatto con la parete posteriore
Non solo la perfetta rotondità, ma anche la variazione di diametro, la geometria, la forma 3D complessa, i fori di diffusione che portano alla lavorazione del foro passante finito possono essere raggiunti con un efficace rilevamento della rottura della parete.
Monitoraggio dell’efficienza della perforazione
L’efficienza di questo dispositivo di monitoraggio con il controllo degli algoritmi consente anche di adattare il processo di perforazione all’usura dell’elettrodo alla situazione effettiva. Ciò consente alla macchina di controllare con precisione la profondità di foratura e di ridurre o eliminare l’impatto della parete posteriore. Inoltre, migliora la velocità di foratura e riduce l’usura degli elettrodi, ottenendo un maggior numero di fori per elettrodo. Sfruttando il nuovo generatore PULSAR, supportato dal dispositivo ADP®, la capacità del controllore di velocizzare la perforazione, migliora l’accuratezza e l’affidabilità del dispositivo di rilevamento della rottura.
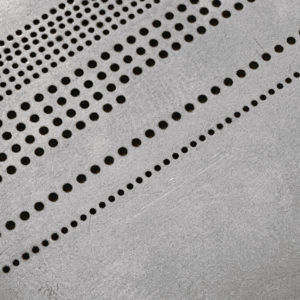
Sebbene i vantaggi di questo processo siano significativi per l’industria aerospaziale, che implica la produzione di grandi quantità di fori, questi vantaggi possono essere applicati anche ad altre applicazioni del mercato della foratura, come il settore medicale, la micro-meccanica o anche l’industria automobilistica…
Fatti e risultati
Perfetto processo di interazione immediata con il muro di rottura
Sensibilità all’angolo di foratura per seguire un profilo di colata complesso
Processo di foratura più rapido ed efficace grazie a ogni caso di foratura adattiva
Certificazione di foratura passante finita
Rilevamento dello sfondamento applicato mediante calibrazione del diametro del foro
SELEZIONE DEL CAMPIONE
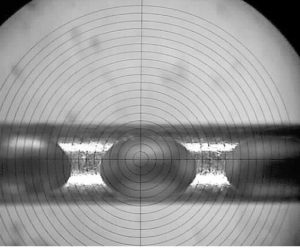

Siamo in grado di rispondere alle vostre sfide di microforatura più impegnative!
Contattateci per una prova gratuita!